Ethanol vs. Hydrocarbons vs. Supercritical CO2 - A Complete Comparative Guide
A Comprehensive Overview of the Most Common Botanical Extraction Solvents
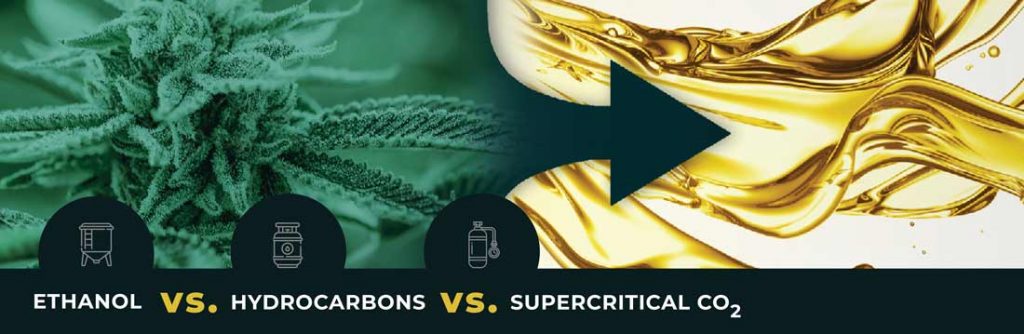
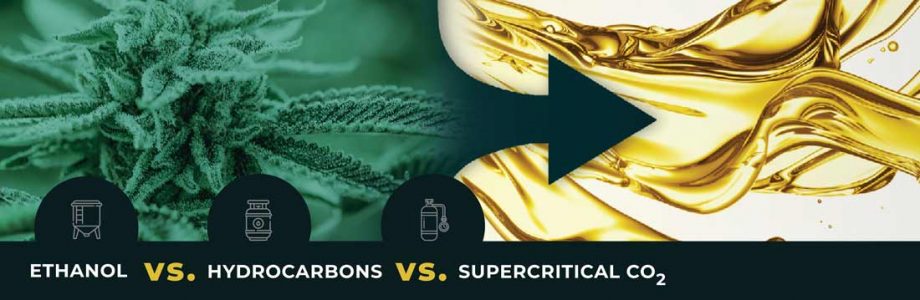
Key Considerations for Selecting a Hemp Extraction Solvent
There are many different solvents available for extraction of botanicals such as hemp. There are advantages and disadvantages to selecting one solvent or another, and it is important for extraction businesses to understand the benefits and drawbacks of the solvent system that they choose.
This article first describes the various criteria that we can use to describe and compare the differences between different solvents. Then we group the common extraction solvents into categories, and explain how each group of solvents compares using these criteria.
“There are advantages and disadvantages to selecting one solvent or another, and it is important for extraction businesses to understand the benefits and drawbacks of the solvent system that they choose.”
Extraction Efficiency
- Solvent extraction is fundamentally the process of:
- Soaking a botanical material in a solvent to dissolve the substances that you are interested in obtaining into the solvent
- Separating the solvent from the plant material
- Recovering your extract from the solvent/extract mixture
- To effectively carry out an extraction process, the selected solvent must rapidly dissolve the target substances present in the plant material, and must be able to maintain a high concentration of the target substance in solution. Always ensure that the extraction solvent chosen satisfies these criteria. Fortunately, most common botanical extraction solvents satisfy these basic criteria.
Extraction Selectivity
- In an ideal world, your solvent would only extract the substance(s) that you desired in your extract and nothing extra, thereby eliminating the need for any additional refining steps after extraction. In reality, extraction solvents are blunt instruments, and only limited selectivity can be achieved. For example, there is not a solvent available that could solvate CBD efficiently, while still leaving THC undisturbed in the plant material. THC and CBD are too chemically similar. There are solvents that will efficiently extract CBD, while leaving behind substantially different molecules like chlorophyll.
Extraction Capacity
- Some extraction solvents are better suited to small scale extraction, while other extraction solvents don’t make much sense unless the extraction capacity required is large.
- Some scale-related factors to consider are maximum allowable quantities (MAQs) for solvent storage, complexity of the process, and the amount of energy that the process requires.
- You will want to select a method that accommodates your current production requirements, and that also hopefully can be scaled up to meet your projected needs.
Extract Characterization
- What products do you wish to produce? Some extraction solvents offer excellent extraction efficiency, but have low terpene retention. Other solvents offer just the opposite. The solvent you select for bulk extract production is probably not the solvent that you would want to select for specialty terpene-rich boutique product manufacturing. Defining the types of products that you wish to produce will help inform your extraction solvent selection.
Post-Extraction Refining Requirements
- Some solvents tend to extract undesirable water-soluble compounds such as proteins, sugars, and gums along with your extract.
- Other solvents leave the water-soluble compounds behind, but have an affinity for fats and waxes that means that more extensive winterization will be required.
- Some extract refining steps are more difficult than others, so your refining requirements should be considered when selecting your solvent extraction method.
Health & Safety
- Many organic solvents can be toxic to operators, and appropriate safety measures will vary depending on the solvent selected.
- Pressurized equipment should be manufactured to internationally recognized standards, such as ASME or PED.
- Many organic solvents are highly flammable. Flammable solvents must be used in equipment that is designed and rated to safely contain and use flammable solvents.
Regulation and Permitting
- Some solvent extraction methods are easier to get local operating permits for than others. Some jurisdictions will only approve certain extraction methods.
- Each solvent extraction method has different regulatory requirements that must be considered.
- Processors should research their jurisdiction’s regulations and work closely with local fire marshals to meet inspection requirements.
Environmental Impact
- Some solvents used in extraction processes can have much larger impacts on the environment than others.
- Regardless of solvent choice, environmental impact will need to be mitigated through responsible use and disposal processes in accordance with environmental regulations.
Equipment Cost
- Equipment cost is obviously a huge variable in selecting an extraction solvent, and cost will vary depending on a number of factors. To name a few:
- As system pressure increases, generally so does the cost of the equipment.
- As extraction temperature decreases, equipment cost generally rises.
- Equipment designed to handle flammable solvents will cost more than similar equipment designed to handle only non-flammable solvents.
- The extraction solvent selected and the size of the equipment are the two primary factors that determine how much equipment capital investment will be required.
Operating Costs: Labor, Utilities, & Solvent Replacement
- Labor and utility expenses are the two main costs associated with extraction processes.
- Manual, labor intensive processes will result in higher COGS for your business.
- All extraction processes require makeup solvent. Solvent is lost through evaporation to the atmosphere, and is also lost by its residual content in the spent botanical material. Solvent consumption rate and solvent cost can be substantial, and should be factored into your solvent selection.
- Utility consumption usually only becomes a significant economic factor when extracting 3,000+ Lbs/day of botanical material. Some solvents inherently require more energy to extract with than others.
Replacement Part Availability
- Avoid “proprietary” technologies or equipment. Solvent extraction is an old and established field, and there are plenty of efficient methods that can be implemented that do not require you to buy into “proprietary” technologies. To date, none of the flashy “proprietary” technologies have offered any overall advantage over common solvent techniques.
- Implement equipment that utilizes well known and respected brands of pumps, valves, control hardware, etc… so that replacement equipment is widely available.
Marketing Impact
- The marketability of a product may be impacted by the solvent used to extract the product.
- For example, CO2 extraction, mechanical extraction, and ethanol extraction can all potentially be marketed as “natural” or “organic” extraction methods and products.
Ethanol Extraction
Ethanol has become the go-to solvent for extractors who are attempting to quickly increase extraction capacity with the lowest capital investment. Ethanol is a strong, medium polarity solvent which causes it to extract a more diverse array of substances than you actually want in your extract. For this reason, most ethanol extracts require post processing to create a high-quality marketable end product.
Ethanol extraction can be performed at either room temperature or low temperature depending on the process flow and desired end products. Ethanol extraction systems are scalable, but there are strict national limits on the amount of flammable liquids one can store or use in a facility. These are called Maximum Allowable Quantities, or MAQs. Often the extraction capacity of an ethanol extraction system is determined by the MAQ rather than any other design requirement.
Extraction Efficiency
Ethanol is a liquid solvent with high solvating power. A well-designed ethanol extraction system will leave approximately 1% residual CBD or less in the extracted material which represents a very effective extraction. The residual CBD content may vary slightly depending on the extraction temperatures, ethanol to biomass ratios, contact time and other mass transfer considerations.
Extraction Selectivity
Extracting with ethanol can be likened to painting with a push broom. As a strong medium polarity solvent, ethanol is highly efficient at extracting almost everything that is in hemp. So while you definitely extract the non-polar compounds that you are looking for such as CBD and terpenes, you also extract a copious quantity of polar compounds such as chlorophyll, sugars, protein etc… The high extraction efficiency reduces extraction times and increases throughput, but at the cost of more post processing requirements to remove the undesired compounds. This is elaborated further in the post-processing section below.
Extracting with ethanol can be likened to painting with a push broom. As a strong medium polarity solvent, ethanol is highly efficient at extracting almost everything that is in hemp.
Extraction Capacity
Ethanol extraction generally can be implemented at any scale, but it is generally the most cost effective to implement at medium extraction capacities of 20 Lbs/Hr to 200 Lbs/Hr of biomass. Below 20 Lbs/Hr, the equipment cost does not really reduce with decreasing extraction capacity. Extracting more than 200 Lbs/Hr generally requires exceeding the general industrial MAQ for ethanol. That means that you must have a facility with H-occupancy (which requires costly facility upgrades) or that you must implement an outdoor processing line (which is not permitted in many jurisdictions). If you do have permission to implement an outdoor system, or if you do have a facility with H-occupancy, then ethanol systems can be implemented with extraction capacities of 1000 Lbs/Hr or more.
Extract Characterization
The crude extract produced by ethanol extraction is usually very viscous, dark in color, and generally a product that requires further refinement. Extracts produced at room temperature are generally green in color without post-processing. Extracts produced at low temperatures have more of a golden-brown hue, but still contain many of the water soluble contaminants that extractors seem to visually associate with green extracts. It is common practice to implement a carbon filtration system right after extraction to remove undesired pigments which darken the extract and render it less marketable.

Ethanol extraction is generally not used to produce boutique, high-value extracts. The ethanol extraction process generally has poor terpene preservation, and the terpene profile of the products may have an “off-odor” due to the contamination caused by the co-extraction of other unwanted substances. Also, since the crude extract is such a crude product, the extract is generally only bought and sold as a feedstock to make distillate or isolate.
The products that are generally produced with ethanol extraction are winterized crude extract, distillate, and isolate.
Post-Extraction Refining Requirement
Ethanol extract can contain two main categories of contaminants that are removed in post-processing before distillation.
The first group is composed of the polar compounds. These compounds may include chlorophylls and other pigments, sugars, proteins and phospholipids/gums). These polar compounds are prone to pyrolysis (high temperature induced degradation) which can cause equipment fouling or discoloration of the final extract. These compounds degrade during extract distillation or solvent recovery, and form hard, charred, carbon-like deposits inside the equipment. The compounds also contaminate distillate, and contribute to dark or red distillate colors. It is common to attempt to remove these polar compounds with a variety of methods including activated carbon filtration, DE filtration, and liquid/liquid washing.
The second group of extract contaminants consists of fats and waxes. Fats and waxes are co-extracted during the ethanol extraction process. Many operators try to reduce the co-extraction of fats and waxes by reducing the ethanol temperature to -40 °F or lower. Low temperature extraction is more expensive to setup and to maintain, but the extract produced by this method has the advantage of generally not requiring any post-processing to remove fats and waxes. Extracts produced with ethanol at room temperature do require post-processing, called winterization, to remove the fats and waxes. Removing fats and waxes is generally easier than removing polar compounds.
Due to the high cost of chilling ethanol solvent to very low temperatures, most large scale extractors operate at room temperature. Much less cooling capacity is required to winterize extract after primary extraction than to cool all of the extraction solvent during extraction.
Due to the reduced amount of equipment and the reduced number of total processing steps, most small capacity ethanol extractors choose to operate their extractors at low temperatures because the reduced complexity is worth the extra expense to them.
Health & Safety
Flammability is the largest safety concern when using ethanol as an extraction solvent. The flashpoint or temperature at which ethanol gives off sufficient vapor to ignite is 55 °F. This means that at room temperature, ethanol will ignite if exposed to an ignition source. Ethanol is classified as a Class IB solvent by the IBC and IFC (International Building Code and International Fire Code) which is the same category as gasoline.
Ethanol can also pose a health risk to employees who are over-exposed to it. Ethanol does have comparatively low health risks when compared with other solvents, but ethanol is still a carcinogenic organic solvent that should be handled with care. Personal Protection Equipment (PPE), such as gloves, eye protection, and respirators, will be necessary when handling ethanol to reduce operator exposure.
It is important to review the Globally Harmonized System (GHS) of Classification for ethanol prior to handling or storage.
Regulation & Permitting
Due to its high flammability, there are established limits in the IBC and IFC (International Building Code and International Fire Code) that regulate the amount of ethanol that can be used or stored in a given area. The occupancy classification of your facility, whether your facility is equipped with sprinklers, and the number of control areas will determine the amount of ethanol that you can have onsite. For example, national regulations stipulate that in an F-Occupancy, only 120 gallons of ethanol can be in closed use within each control area. This amount will double if certified automated sprinklers are in place throughout the building. It is important to check your state and local requirements as well, because certain jurisdictions have enacted standards that deviate from the national regulations.
Any equipment that is used for ethanol extraction should be Engineering Peer Reviewed and approved by a licensed professional engineer to ensure the equipment complies with the pertinent regulations and safety protocols.
Environmental Impact
Ethanol has been granted a ‘green circle’ by the EPA’s Safer Chemical Choice database based on the limited dangers posed by ethanol when compared to other solvent options, meaning ethanol has lower health and environmental risks than many other common solvents.
Ethanol is mainly lost to the environment as residual liquid content in spent biomass, and as vapor that is released or lost during transfers or open air handling of solvent. The gaseous or vaporous emissions are generally small. Significant amounts of liquid solvent may be retained in spent biomass, and careful disposal of ethanol contaminated material is important.
Equipment Cost
Ethanol extraction systems operate at low pressure and are thus usually much more affordable to manufacture at small to moderate scale than CO2 extraction systems of the same capacity. Ethanol extractors are also comparatively simple to operate and maintain. Replacement parts and fittings are widely available.
The major equipment components required to make crude extract by ethanol extraction are: material preparation equipment, extraction equipment, solvent recovery equipment, and supporting heating and cooling equipment. Two additional pieces of equipment, post-extraction biomass dryers and solvent rectification systems, may be required and are discussed in the “Additional Considerations” section below.
“All factors considered, ethanol extraction provides the most extraction capacity (Lbs/Hr) per dollar invested in extraction equipment at capacities ranging from 100-2500 Lbs/day.”
The downside of ethanol extraction is that the crude extract produced by this method is generally not a high value product without further refinement. Additional post-processing such as winterization, degumming and molecular distillation may be required to manufacture a higher-value, more refined extract. As noted earlier, some operators try to avoid this by extracting at temperatures of -40 °F or lower in an attempt to make a better quality CBD crude extract. However, the colder the extraction temperature, the greater the equipment cost required to achieve it. Whether the quality improvement is worth the increased capital and operating expenses is debated.
All factors considered, ethanol extraction provides the most extraction capacity (Lbs/Hr) per dollar invested in extraction equipment at capacities ranging from 100-2500 Lbs/day. At larger scales, the extra capital required for the large dryers, low temperature chillers, and facility buildout begin to make CO2 extraction a cost competitive alternative to ethanol extraction.
Operating Costs: Labor, Utilities & Solvent Replacement
Ethanol extraction is generally labor intensive. It is conducted as a batch process at scales up to several thousand Lbs/day of biomass. At this scale, operators usually manually perform the following steps: grind the biomass, pack the biomass in bags, load the bags into ethanol extractors, unload the bags, unpack the bags, and dispose of the biomass. At capacities above 3,000 Lbs/day, more automated processes can be implemented to reduce labor, but the equipment cost is increased.
All extraction techniques require solvent recovery. Ethanol requires more energy per gallon to recover than any of the other common solvents such as butane, propane, hexane, heptane, or CO2. This difference is negligible with small production volumes of less than 1,000 Lbs/day of biomass. Above this amount, you start to notice the increased utility consumption required to operate an ethanol extraction process when compared to other options. The utility expenses do not generally become a significant portion of the total extraction operating expenses until you are processing 3,000 Lbs/day or more. Above this amount, it may pay to consider other extraction solvent options.
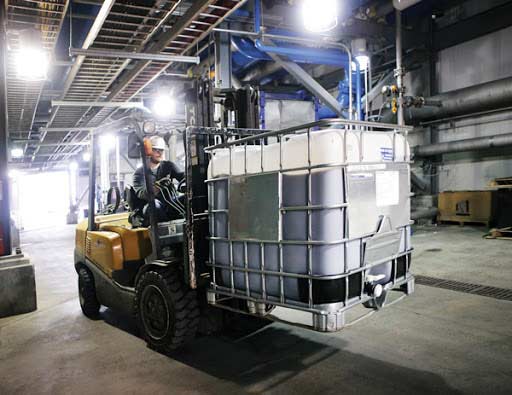
One of the highest sources of operational expense with ethanol extraction systems is the replacement cost for the ethanol solvent. Ethanol solvent is lost in the spent biomass. The spent biomass absorbs it, and the methods used by most extractors to recover it do a very incomplete job. The ethanol itself (pre-tax) generally costs around $8-16 per gallon in bulk with additional cost for taxes. Ethanol is taxed in the USA if the ethanol cannot be proven to be used and lost to an industrial process. Providing this “proof” to the federal government is not an easy process. At the time this article was written, the tax rate for consumable grade 190 proof ethanol was $25.35 per gallon.
See “Additional Considerations” below for a more detailed explanation of how much solvent is lost, and how to mitigate these losses.
Replacement Part Availability
Room temperature ethanol extraction equipment replacement parts such as valves, fittings, gaskets, and other wear components are widely available. Components for low temperature ethanol extraction equipment are harder to find and cost more because the parts must be designed to function at very low temperatures.
Marketing Impacts
Ethanol extracts that are produced using organic ethanol can be marketed as organic products. Ethanol extraction and CO2 extraction are generally regarded as the two “greenest” extraction processes.
Additional Considerations
Businesses that choose to implement ethanol extraction will need to consider drying methods to remove ethanol from the spent biomass. Spent biomass can contain upwards of 50% solvent by mass if nothing is done to reduce the amount left in the biomass following extraction. A residual solvent content of 50% in your spent biomass would mean that you lose 1000 Lbs of ethanol (about 150 gallons) for every 1000 Lbs of biomass you extract. This is tough on your business economics. High residual ethanol concentrations in spent biomass create a fire risk and require hazardous material disposal (the biomass cannot be disposed of as general waste in a dumpster.)
Ethanol extraction companies have implemented screw presses, centrifuges, and thermal dryers to reduce the amount of residual solvent in the biomass. Screw presses and centrifuges reduce the residual ethanol to a limited extent (roughly ~25%-35% residual ethanol by mass) while biomass dryers can reduce the solvent content to levels below 0.5% by mass. While 25% residual solvent improves process economics, it does not eliminate the hazards or waste disposal issues mentioned above. Regardless, most small companies choose to use either centrifuges or screw presses to reduce the residual ethanol content, because the capital expense for a dryer is much higher. Many small companies also try to circumvent the hazardous waste disposal requirement, but regulators across the nation are increasingly flagging this problem and requiring that it is properly dealt with.
Another often overlooked consideration when evaluating ethanol extraction is that ethanol is miscible (fully soluble) with water. Plant material contains water, so as you repeatedly recover and reuse your extraction solvent it can become gradually diluted with water. Dilution with water reduces extraction efficiency, so the water may need to be routinely removed from the solvent using a distillation column or desiccant materials. Drying your biomass as much as possible before extraction will help reduce water accumulation in your solvent. Problem prevention is more economical than the cure in this case.
Hydrocarbon (Butane & Propane) Extraction
Applying a moderate amount of pressure (up to 250 PSIG) to hydrocarbons like butane or propane forces them from a gas to a liquid state. Once they are in this dense liquid form, these compounds act as potent, non-polar extraction solvents. Butane and propane have become popular solvents for extractors who seek to create a crude extract that requires minimal post processing and that is rich in terpene content.
Butane and propane extraction can be performed at either room temperature or low temperature depending on the desired end products. Both solvents are highly flammable and heavily regulated, which poses unique challenges for the design and buildout out of the extraction facility.
Extraction Efficiency
Butane and propane are selective non-polar solvents with slightly reduced extraction efficiency when compared against ethanol or CO2 extraction. The slightly reduced solvent power does not prevent high extraction efficiency, it just means that the butane extraction operator might have to wash the same materials more than once during an extraction process, or might have to re-extract the same material to achieve the same extraction efficiency as CO2 or ethanol methods.
Butane/propane extraction efficiency at room temperature is higher than butane/propane efficiency at low temperatures. Room temperature extractions will have a higher extraction efficiency (leaving less CBD in the biomass) but will have greater fat and wax content in the crude extract. On the other hand, cold hydrocarbon extracts can be produced with very little fats or waxes at the expense of extraction efficiency.
Extraction Selectivity
Butane and propane are non-polar solvents that are much more selective than ethanol for the compounds generally desired in a botanical extract. The extracts produced with butane/propane extraction generally have more valuable characteristics than those produced with ethanol. The extracts contain little to no contaminants such as sugars, proteins, and phospholipids. The extracts have a high content of CBD or other active botanical ingredients, as well as higher terpene content than most other types of extracts. If the extraction is conducted at room temperature, non-polar fats and waxes will be co-extracted with the CBD and terpenes. These can be removed via winterization. Minimal fats and waxes are co-extracted at very cold temperatures. Extraction at very cold temperatures with butane or propane can produce extracts that do not require any post processing to sell.
Extraction Capacity
Hydrocarbon extraction is usually best suited to smaller extraction capacities. Economical, practical, and compact systems are readily obtained for extracting between 50 and 500 Lbs/day.
“Hydrocarbon extraction is usually best suited to smaller extraction capacities. Economical, practical, and compact systems are readily obtained for extracting between 50 and 500 Lbs/day.”
This is primarily due to the nationally stipulated MAQs (Maximum Allowable Quantities) of 150 Lbs butane and propane per control zone that can be stored or used in a general industrial facility. Much larger capacity systems can be manufactured, but require either an H-occupancy control area, or outdoor implementation. Creation of an H-occupancy area is very expensive, and the jurisdictions that will allow outdoor butane extraction of hemp or other botanicals are limited.
Extract Characterization
Extraction temperature and other factors influence the properties of hydrocarbon extracts. Some hydrocarbon extracts are terpene rich, light in color, and low in fats/wax content. Other extracts may be opaque, may contain a substantial amount of fat/wax, and may be dark brown in color. A wide range of products can be produced using propane/butane extraction by changing the type of botanical material extracted, the material preparation method, the extraction temperature, extraction duration, and other factors. Propane/butane extraction is the only extraction method that produces such a wide range of different types of extracts, and it is the only extraction method that produces extracts that have high value without any substantial post-processing steps.
Common End Products Include:
- Shatter
- Budder
- Crumble
- Wax
- Rocks & sauce
- Flan
- Live resin
- Cured resin
- Crude extract
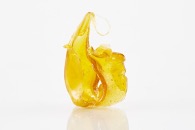
Propane & butane extraction can be used to produce extracts that have higher terpene content than any other extraction method. The boiling points of butane and propane are very low. Propane and butane can be recovered at low enough temperatures that the terpenes do not evaporate with the solvent, and are therefore better preserved in the final extract. Since recovery of these solvents occurs at low temperatures, the terpenes are also not damaged by high temperatures like those experienced during ethanol recovery.
Post-Extraction Refining Requirement
Hydrocarbons are non-polar extraction solvents, so extracts produced with butane or propane usually contain only negligible amounts of equipment-fouling phospholipids, sugars and proteins. These extracts typically do not require any post processing to remove these fouling compounds.
Similar to ethanol, the post-extraction refinement requirements for fats and waxes will depend upon the extraction temperature. Some operators extract at temperatures below -40 F to avoid co-extracting fats and waxes. Extracting at temperatures this cold will generally prevent the operator from needing to post process the extract to remove the fats and waxes. Room temperature hydrocarbon extraction will require post-extraction winterization to remove fats and waxes.
Regardless of extraction temperature, small quantities of residual butane/propane must be removed from the extract. To accomplish this, the operator usually places the extract in a vacuum oven and controls the temperature and pressure to remove butane/propane from the finished extract.
Health & Safety
Both butane and propane are flammable gases that pose high fire and explosion risk if mishandled. These solvents present the highest fire risk of any solvent discussed in this article. Any facility that utilizes hydrocarbon extraction should do so ONLY in a C1D1 explosion proof extraction booth or room that has been professionally designed and engineered. All propane or butane extraction equipment should be reviewed, approved, and stamped by a professional engineer.
From a health perspective, hydrocarbon solvents can range from being moderately benign to being quite neurotoxic and carcinogenic. Butane and propane are relatively non-toxic, but the air inside the extraction facility should be monitored to prevent operators from being routinely exposed to substantial quantities of either solvent. Routine exposure even to comparatively non-toxic hydrocarbon solvents can have lasting health consequences.
Hydrocarbon solvents come in many different grades. They are produced first and foremost as fuels, and as such, sometimes contain additives or contaminants that are much more toxic than the solvent itself. It is critical to source hydrocarbon solvents from a vendor which can document that the solvents are free from contaminants which may harm operators or end-users.
Regulation & Permitting
Regulations for propane & butane extraction vary by state and municipality, with some municipalities having banned propane/butane extraction entirely. You can expect to experience a heightened level of scrutiny and oversight when implementing a propane/butane facility because the risk of fire or explosion is higher than it is with other extraction methods.
There is also a lingering negative stigma around this extraction method caused from disastrous events caused by unlicensed, irresponsible operators performing dangerous extractions. The numerous fires and injuries caused by these unlicensed hydrocarbon facilities have caused regulators to be wary of hydrocarbon operations.
Despite the stigma, hydrocarbon extraction is safe when conducted properly with professionally engineered equipment. In fact, hydrocarbon extraction is utilized safely and successfully at large scale not only in hemp extraction, but in other industries such as essential oil extraction, cacao extraction, and petroleum refining.
Before implementing this form of extraction, be sure to meet and collaborate with the local fire marshal and other regulatory authorities. A little goodwill can go a long way.
Environmental Impact
The environmental impact of propane and butane is also comparatively benign, as both compounds have a short half-life in the atmosphere and eventually degrade to CO2. That said, both solvents are still potent greenhouse gases, and their release to the environment should be prevented and carefully controlled. Since these solvents are gases under most conditions experienced around the globe, they do not have the same potential to pollute surface and groundwater as other liquid solvents.
Equipment Cost
Hydrocarbon extraction equipment is very economical at small scale. However, the facility buildout required to meet the fire marshal’s requirements may substantially increase the cost of the complete extraction installation.
“Hydrocarbon extraction equipment is very economical at small scale. However, the facility buildout required to meet the fire marshal’s requirements may substantially increase the cost of the complete extraction installation.”
Additionally, pursuing low temperature extraction will substantially increase equipment costs. Solvent temperatures below -40° F will see a jump in price because standard valves and seals will not work at these temperatures and must be substituted for more expensive components. Low temperature refrigeration systems needed to chill the solvent add significant cost as well.
Operating Costs: Labor, Utilities & Solvent Replacement
Butane extraction is a batch process, so it is inherently somewhat labor intensive. Operators typically grind the biomass, pack it into bags, load the bags into the extractors, pull it out of the extractors, unpack the bags, and then dispose of the biomass manually. The amount of labor required is comparable to batch ethanol extraction.
Utility costs are generally lower for butane extraction than for ethanol or CO2 extraction. Butane is an energy efficient solvent to recover and reuse. This helps keep operating costs down. Chilling butane to super low temperatures for extraction reduces the energy efficiency of the process.
Butane extraction solvent consumption varies widely. Cold extractions result in a large amount of lost solvent because the cold liquid solvent remains caught up in the spent biomass. It warms up and vaporizes within a couple of hours after extraction, so you do not have the same disposal problems as with ethanol extraction. Room temperature extractions have very little solvent loss, because the solvent can be vaporized and recovered out of the biomass in the extraction equipment.
High purity butane solvent is expensive, so your extraction solvent bill does constitute a significant portion of your operating expenses when you are performing cold extractions. If you are performing room temperature extractions, then the cost of replacement solvent is moderate.
Replacement Part Availability
Replacement parts for butane/propane extraction systems that operate at temperatures above -40 F are widely available and economical. Low temperature hydrocarbon systems that operate below -40 F require more expensive and specialized valves, fittings, and seals, which make the parts less available and more expensive. The availability of parts for butane/propane extraction systems is comparable to the availability of parts for ethanol extraction systems operating at similar temperatures, and more available than the high pressure parts used in CO2 extraction equipment.
Marketing Impacts
Extracts produced by hydrocarbon extraction cannot be marketed as organic products. Some consumers of botanical extracts may be wary of products made using chemical solvents. Butane/propane extraction is not generally considered a “green” extraction technology despite the fact that this extraction technique has a relatively small environmental impact.
Supercritical CO2 Extraction
Carbon dioxide is a gas at room temperature and pressure. When compressed under high pressure (2,000 to 5,000 PSIG) the substance becomes what is known as a supercritical fluid. A supercritical fluid is a phase in which the molecules have the density of a liquid but still have the movement properties of a gas. A fluid in this state can penetrate deep into a botanical matrix, can pass through tightly packed beds of botanical material, and can dissolve a substantial amount of non-polar substances. Supercritical CO2 extraction technology provides an efficient extraction method that provides good extraction efficiency, low operating cost, and a product that can be marketed as both “green” and organic. Local regulators are almost always very amenable to the implementation of a CO2 extraction facility because they perceive the process as being safer than processes that require flammable materials. Additionally, CO2 extraction produces extracts that are of high-quality and thus require less post-processing than extracts produced by ethanol extraction. While CO2 extraction can produce extracts of excellent quality, the equipment comes with a high cost to purchase and operate, especially at small to moderate scale.
Extraction Efficiency
Supercritical fluids, including CO2, have unique properties that simultaneously give them liquid-like density and gas-like movement properties. Combined, these qualities make them incredibly effective at solvating botanical material and result in high extraction efficiency. A well-designed Supercritical CO2 extraction system will leave approximately 1% residual CBD or less in the extracted material.
Extraction Selectivity
Supercritical CO2 is a highly non-polar solvent of moderate strength and will effectively extract non-polar compounds from hemp such as fats, waxes, CBD, and terpenes. Supercritical CO2 extracts are known for having a high fat and wax content when compared to the other solvents. All extracts produced by this method require winterization.
CO2 is a solvent that possesses tunable extraction strength and selectivity. By manipulating extraction pressure and temperature operators can produce a wider variety of extracts than is possible with ethanol extraction. Lower pressures result in extracts that are lighter in color and flavor. Higher pressures result in faster, more complete extractions, but at the cost of a darker extract color.
CO2 extracts are mainly produced as a base extract for distillation into more refined products such as distillate and isolate. The extract is sometimes put into vape pens and other consumable forms after only winterization, but this is growing less and less common. As a base extract for distillation or other further processing, CO2 has good market value because it has good purity, and lacks troubling contaminants such as sugars, proteins, gums, and other more polar molecules.
Extraction Capacity
Supercritical CO2 systems have extraction capacities that range from 25 to 55,000 Lbs/day, and tend to be ideal for processors working with volumes of 1,200 Lbs/day or greater. The reason for this is that the high-pressure components are expensive, and the cost of the components does not decrease linearly with decreasing size. This causes a good quality CO2 extractor to be much more expensive than any other technology when implemented at capacities below 1,200 Lbs. As the extraction capacity required increases, CO2 extraction becomes a very cost competitive option. At capacities larger than 5,000 Lbs/day, the cost of a carbon dioxide extraction system is only slightly more expensive than the cost of flammable gas or liquid plants.
The capacity of these systems is increased as the extraction temperature, extraction pressure, and flowrate of carbon dioxide increases. There is no de-facto limit for the scale of extraction that can be implemented with supercritical carbon dioxide.
Extract Characterization
Generally, supercritical CO2 extracts are high-quality, and are low in phospholipids, sugars, and proteins. Extracts created using lower pressure CO2 are usually light in color and can be marketed as a finished product after they are dewaxed. Higher pressure extractions usually require some additional refining due to their darker color.
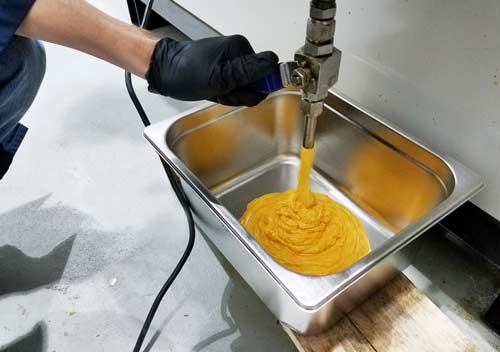
Common end products produced via CO2 extraction are CBD crude extract, CBD raw vape pen extract, CBD distillate, and CBD isolate.
Processors using CO2 can manipulate extraction parameters to produce extracts rich in terpenes. Often, a processor will perform an initial extraction at low temperature and pressure with CO2 to capture the terpenes. The terpene fraction can be collected, and then the pressure and temperature can be increased to increase extraction speed and efficiency. This capability to use pressure to change the strength of the extraction solvent is a characteristic unique to CO2 extraction.
Post-Extraction Refining Requirement
A winterization (dewaxing) step will be necessary to remove the fats and waxes that are extracted. This is usually the only refining step necessary to produce a salable crude extract using carbon dioxide extraction. Sometimes an operator will incorporate a carbon filtration process into their winterization procedure to lighten the color of extracts produced at higher pressures and temperatures. Overall, the post-processing required to market and sell CO2 extracts is reduced when compared with the post-processing required to sell ethanol extracts, and increased when compared with what is required for butane/propane extracts.
Health & Safety
There are three major safety and health concerns associated with CO2 extraction: asphyxiation, explosion, and low temperature exposure.
The first and most apparent risk is asphyxiation. CO2 in high concentrations (greater than 10,000 PPM) can reduce your body’s ability to uptake and use Oxygen. The atmospheric concentration of CO2 is about 400 PPM, so a well ventilated space will be very hard pressed to reach this high concentration. Events that might cause high carbon dioxide concentrations are an overpressure safety relief valve discharging carbon dioxide into your work environment, or seals failing catastrophically. You should always pipe over pressure safety valves to outside the facility. Seal failures can be prevented with good maintenance practices. In any case, it is important to conduct CO2 extraction in a well ventilated space, and to install CO2 alarms and meters in your facility.
The second most prevalent risk is due to the inherent high pressure present in the system. If a system is inappropriately designed or manufactured, there is a risk of a catastrophic failure of a high pressure vessel or component. Many CO2 extraction systems operate at pressures as high as 5,000 PSIG, and a catastrophic vessel failure could easily kill anyone nearby. The American Society of Mechanical Engineers (ASME) has developed calculations and tests to prove that a pressure vessel is safe for the rated pressure use. It is critical to use ASME stamped vessels and safety devices for all pressurized systems. Some imported systems are not ASME approved, and do not meet these engineering standards.
The third risk comes from CO2 being a potent refrigerant that has the ability to cause frostbite if handled inappropriately. If high-pressure CO2 is discharged to atmospheric pressure, it has the potential to become extremely cold. Protective equipment, like leather gloves and safety glasses as well as proper safety protocols must be followed for operator safety.
Regulation & Permitting
CO2 extraction is the least scrutinized extraction method discussed in this article. Regulators usually like to confirm that the equipment has been reviewed by a PE, that the equipment has ASME approved pressure vessels, and that the facility has carbon dioxide detectors and adequate ventilation in it. Beyond that, most regulators show minimal interest.
CO2 is non-flammable, non-toxic, and less damaging to the environment than other extraction methods. Because CO2 extraction doesn’t use the flammable liquids or gases that commonly limit other processes, there is not a real “cap” on CO2 extraction capacity. There are several active carbon dioxide extraction plants in the USA that can process more than 50,000 Lbs/day of botanical products.
Environmental Impact
Carbon dioxide extraction is considered to be a “green” technology because the solvent is non-flammable, has comparatively low impact on the environment, and is non-toxic. The environmental impact of CO2 extraction is low because the carbon dioxide is reused multiple times within the system, and has a lower greenhouse gas potential than hydrocarbons or other solvents when some is released to the atmosphere.
Equipment Cost
CO2 extraction equipment is more expensive than other types of extraction equipment, especially at small scale. The high pressure valves, seals, components, and ASME pressure vessels all cost more than the lighter, general duty equipment used to make the other types of extraction equipment. As the equipment scale gets larger, the cost difference between implementing CO2 extraction and the other types of extraction mentioned in this article decreases. Scaling processes that utilize flammable solvents becomes expensive due to the high cost of complying with increasingly stringent fire and explosion prevention regulations. Scaling CO2 extraction becomes less expensive as the equipment gets larger because the equipment cost does not increase linearly with size.
CO2 extraction becomes worth considering on a cost basis at about 1,200 Lbs/day of extraction capacity. It is still more expensive than other technologies at this capacity, but if you can achieve slightly higher market value for the product, then it begins to make economic sense. Above ~5,000 Lbs/day, supercritical carbon dioxide extraction is very competitive with technologies that utilize flammable solvents, and should be considered as a primary option for the project.
Above ~5,000 Lbs/day, supercritical carbon dioxide extraction is very competitive with technologies that utilize flammable solvents, and should be considered as a primary option for the project.
CO2 extraction is exceptionally hard on equipment. Make sure that your manufacturer took time to specify high quality components from reputable manufacturers. At Aptia, we deliberately utilize high-quality European, Canadian, and American valves, pumps, and other components in our CO2 extractors to give the product excellent reliability.
Operating Costs: Labor, Utilities & Solvent Replacement
The labor required to operate a large CO2 extractor generally is reduced when compared with ethanol or butane extraction. The material is dry and free of flammable solvents during the process, which enables operators to handle the material pneumatically to reduce labor. Batch sizes are also usually increased, which reduces the amount of labor per Lb extracted. A third advantage is that CO2 extraction lends itself to automation. Most of these extraction systems are automated, and only require active operator intervention for loading and unloading.
CO2 extraction consumes a substantial amount of electricity to operate refrigeration equipment and pumps. These systems sometimes also consume natural gas to provide heating. The utility consumption of a CO2 plant is higher than that required for a comparably sized butane plant, and lower than that required by an ethanol plant. Overall, the cost of the electricity and natural gas required to operate one of these systems is very economical when placed in the context of the whole extraction business, but comprises a significant part of the total operating expenses.
Only a small amount of solvent is lost with each CO2 extraction, and the cost of replacing solvent is the lowest out of any method discussed in this article. Carbon dioxide is the cheapest of all the solvents to purchase, and may cost as little as $0.25 per pound for large clients.
Overall, CO2 extraction has low operating costs when compared to propane/butane or ethanol extraction processes. Propane/butane operating costs are similar to carbon dioxide costs when the propane/butane process is conducted warm to prevent solvent loss. Carbon dioxide extraction is generally more economical at scale to conduct than ethanol extraction.
Replacement Part Availability
Replacement parts and seals for CO2 extractors are not available as off-the-shelf goods. These components are almost always specially designed to handle the extreme pressures encountered with this extraction method. A supercritical CO2 extraction business should always collaborate with the equipment manufacturer to ensure that a sufficient stock of common replacement goods is kept on hand to prevent undesired downtime.
Marketing Impacts
Extracts produced by this method may be able to command a higher price in the marketplace. The production method is considered clean, green, and organic. Existing brands that produce mainstream consumer goods want to present consumers with a product that does not incorporate any products produced in a manner that might decrease consumer confidence. If your business model counts on selling extracts to existing, large consumer retail product manufacturers, then CO2 extraction should be considered when you select your extraction system.
Uncommon Solvents
Use of solvents beyond those described above is uncommon. It is important for us to briefly address some solvents that were historically used, but that have been phased out due to their health effects or environmental consequences in case you run across them.
Halogenated (chlorinated or flourinated) solvents are generally much more toxic than hydrocarbon solvents and are not recommend for use in botanical extraction. These solvents were successfully used in the past, but have been largely or completely phased out. Extraction facilities that used these solvents have been decommissioned due to consumer pressure, environmental regulations, or worker health safety concerns. These solvents can cause serious environmental contamination and damage that last for decades or longer. These solvents are the cause of many nationally recognized superfund sites that will require fortunes to cleanup, because these solvents were often used and spilled during machine manufacturing more than 70 years ago.
“Proprietary” or “novel” extraction equipment that utilize chlorinated or fluorinated refrigerant gases seem to sporadically pop up. DO NOT USE CHLORINATED OT FLOOURINATED REFRIGERANT GASES FOR EXTRACTION. These gases are considered persistent environmental pollutants, and are potent greenhouse gases that have global warming potentials 3600-12000x greater than carbon dioxide. That means that releasing 1 Lb of one of these gases into the atmosphere can have the equivalent detrimental impact on the environment that releasing 6 Tons of carbon dioxide! If this isn’t bad enough, the use of these chemicals is regulated super rigorously by the EPA. The EPA fines department stores and other businesses that suffer from occasional leaks of these refrigerants–these fines are often in the millions of dollars. All extraction processes lose some of their extraction solvent in spent biomass, so implementing an extraction process using one of these solvents is not only grossly irresponsible, it is subject to potential legal action and fines from the EPA and other government agencies. People are lured into the idea by “innovators” who sell them outrageously priced equipment to conduct “proprietary” extraction processes with these refrigerant gases. Using these gases is not a new idea, does not have any significant advantages over the common solvents used today, and is not common because these solvents have massive downsides.
Solvent Comparison Summary Reference Chart
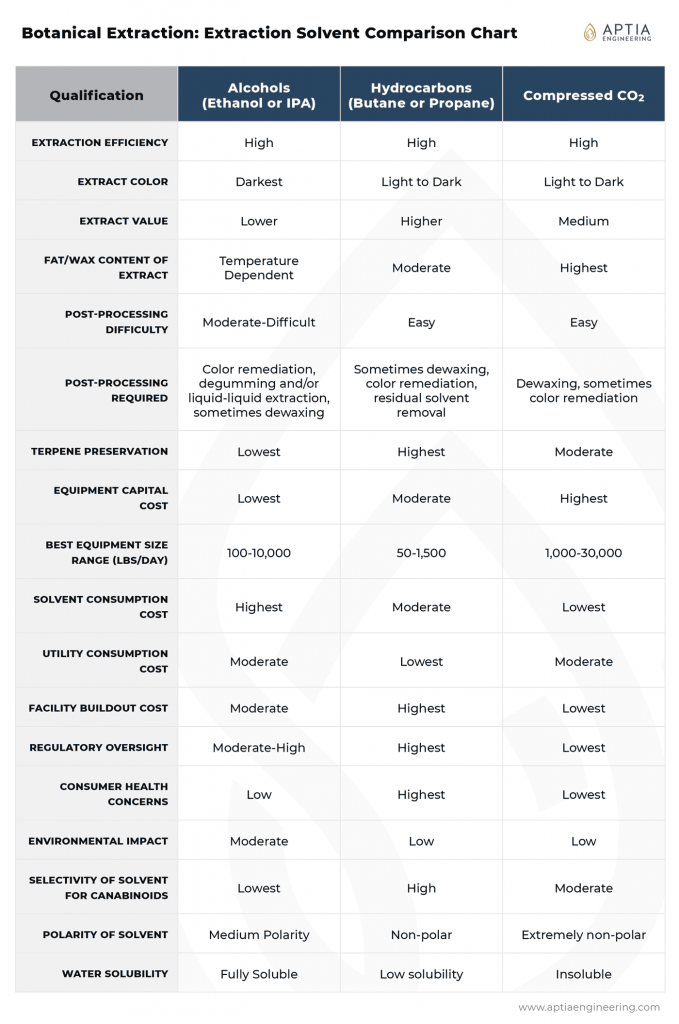
- Published by Aptia Engineering on May 10, 2021